Elevating Miami’s Skyline: The Power of Perforated Metal Panels and Architectural Louvers
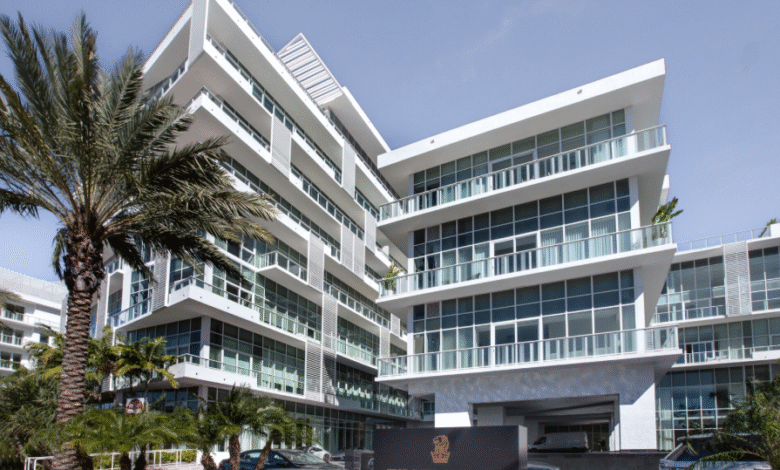
Miami’s built environment is a vibrant tapestry of light, color, and innovation. From the sun-drenched façades of high‑rise condominiums to sleek commercial structures lining Biscayne Boulevard, the city thrives on bold design and performance-driven materials. For architects and developers seeking to make a lasting impression—and property owners craving superior building longevity—the choice of exterior cladding is critical. Two standout solutions dominate modern façade architecture: the perforated metal panel and architectural louvers. This guest post explores their unique benefits, how to integrate them into Miami projects, and what to look for when hiring a professional façade installer in Miami.
Why Façade Design Matters in Miami
Miami’s tropical climate and coastal conditions present both an opportunity and a challenge. Balmy temperatures, high humidity, and intense sun demand materials that deliver:
- Thermal performance to reduce cooling loads
- Corrosion resistance in a salt‑air environment
- Sun shading to control glare and heat gain
- Aesthetic versatility to meet diverse architectural visions
By selecting the right façade system, architects can craft structures that not only withstand Miami’s climate but also enhance occupant comfort and energy efficiency. Perforated metal panels and architectural louvers offer a synergy of form and function perfectly suited to the Magic City’s evolving skyline.
Understanding Perforated Metal Panels
What Are Perforated Metal Panels?
A perforated metal panel is a sheet of metal—often aluminum, stainless steel, or corten steel—punctured with an array of geometric holes or patterns. These perforations can range from simple round holes to intricate, custom-designed shapes that serve both practical and artistic purposes.
Key Advantages
- Ventilation and Airflow
The perforations allow natural air movement, enhancing passive ventilation strategies. In parking garages or mechanical rooms, these panels can maintain airflow without sacrificing security or aesthetics. - Sun and Glare Control
Strategically sized and spaced holes filter sunlight, reducing heat gain and glare. This creates dramatic light-and-shadow effects within interior spaces, enlivening environments without compromising thermal comfort. - Lightweight Durability
Made from high-performance alloys, these panels are both lightweight and robust. Aluminum panels resist corrosion in Miami’s humid, salty air, while corten steel develops a stable, rust-like patina that protects against further degradation. - Customizable Aesthetics
From straightforward grids to bespoke patterns inspired by natural or cultural motifs, perforated panels enable architects to craft façades that tell a story. Laser-cut precision ensures consistency across large expanses of cladding. - Noise Reduction
In conjunction with acoustic backing materials, perforated panels can dampen external noise, making them ideal for waterfront properties or busy urban corridors.
Applications in Miami
- High-rise residential towers: Channel sea breezes while offering solar shading.
- Parking structures: Provide ventilation and security without bulky grilles.
- Retail façades: Capture attention with dynamic patterns and backlighting.
- Institutional buildings: Merge public art and building envelope in libraries or museums.
See also: Mastering Funnel Growth to Skyrocket Your Conversion Rates
Exploring Architectural Louvers
Defining Architectural Louvers
Architectural louvers are horizontal or vertical slats—typically of aluminum, steel, or fiberglass—designed to admit air and light while excluding rain, direct sun, or noise. Louvers can be fixed or adjustable, operable by manual or automated systems.
Core Benefits
- Sun Shading and Energy Savings
Louvers block high-angle sun rays, reducing the solar heat gain coefficient of glazed areas. This translates directly into lower air conditioning loads and enhanced occupant comfort. - Ventilation Control
Operable louvers allow users to control airflow, opening during cooler hours to leverage natural ventilation. In mechanical spaces, fixed louvers ensure consistent air exchange without letting weather in. - Weather Protection
Designed to shed rainwater, louvers safeguard inner walls and mechanical equipment. Properly pitched blades direct moisture away while maintaining airflow. - Architectural Accent
Louvers lend buildings a sleek, layered look. By varying blade profiles, depths, and finishes, designers can craft striking shadow lines and horizontal emphasis. - Durability
Marine-grade aluminum and powder-coated finishes deliver outstanding corrosion resistance in beachfront environments.
Miami Use Cases
- Commercial office towers: Integrate louvers with curtain wall systems for daylight control.
- Hospitality projects: Use operable louvers on balconies or terraces for flexible indoor-outdoor experiences.
- Infrastructure: Conceal cooling towers, exhaust openings, and service areas with louvers that blend seamlessly into the façade.
Harmonizing Perforated Panels and Louvers
Combining perforated metal panels with architectural louvers unlocks layered façades that perform on multiple fronts. Consider these integrated strategies:
- Dual-function screens: Use a perforated panel outer layer for visual interest, backed by a louvered sub-fin to optimize shading and airflow.
- Zoned sun control: Position louvers on south and west façades for rigorous sun blocking, while employing perforated panels on east façades to welcome morning light.
- Backlit effects: Illuminate perforated metal panels at night to cast louver silhouettes, creating dynamic displays that animate after dark.
This multi-tiered approach not only maximizes environmental control but also grants architects an expansive toolkit for crafting signature façades.
Selecting a Professional Façade Installer in Miami
Choosing the right installer is as pivotal as selecting quality materials. Look for these criteria when vetting façade contractors:
- Local Expertise
Miami’s building codes, hurricane regulations, and permit processes demand local know‑how. A seasoned installer will navigate zoning ordinances, wind load requirements, and coastal construction standards with confidence. - Proven Track Record
Ask for a portfolio demonstrating successful installations of perforated metal panels and architectural louvers. Seek testimonials from past clients and inspect installed sites in person, if possible. - Engineering Collaboration
Complex façades often require structural calculations and wind-load analysis. A top‑tier installer should have in‑house or partnered engineers to certify designs and ensure compliance with Miami-Dade County hurricane codes. - Material Proficiency
From alloy selection to finish application, the installer’s familiarity with specialized coatings, anodizing, and weather-resistant treatments is vital. Confirm they work with mill certificates and material testing to guarantee performance. - Installation Techniques
Precision mounting systems—like adjustable standoffs, rail systems, or concealed clips—are essential for achieving seamless panel alignment and accommodating building movement. - Quality Assurance and Warranty
A rigorous QC program—complete with thermal imaging, water testing, and site inspections—demonstrates commitment to durability. Ensure clear warranty terms covering materials and workmanship. - Project Management
Timely delivery, on‑site safety protocols, and effective communication reduce costly delays. An installer who integrates BIM coordination and uses digital tracking tools will keep large-scale projects on schedule.
Navigating Miami’s Coastal Conditions
Miami’s unique environment tests façades like few others. Salt spray, high humidity, and hurricane-force winds require material and design strategies tailored to coastal resilience.
- Corrosion mitigation: Opt for marine-grade aluminum or stainless steel alloys with enhanced anodic coatings.
- Wind load engineering: Panels and louvers must withstand up to 180 mph wind speeds in designated hurricane zones. Proper attachment systems and embedment details are non-negotiable.
- Thermal expansion: Temperature swings from sun exposure can cause metal movement. Allow for expansion joints and floating mounts to prevent buckling or warping.
By partnering with an installer experienced in waterfront projects, clients ensure their façades will endure, protecting investments for decades.
Sustainability and Energy Performance
Beyond aesthetics and durability, perforated panels and louvers contribute to green building goals:
- Daylighting: Perforated panels diffuse sunlight, reducing reliance on electric lighting while maintaining glare control.
- Natural ventilation: Louvers enable operable openings, cutting HVAC run‑times during cooler periods.
- Locally fabricated: Sourcing panels and louvers from regional manufacturers minimizes transportation emissions.
- Recyclable materials: Aluminum and steel are highly recyclable, supporting circular economy principles.
These strategies align with LEED, WELL, or other sustainability rating systems, helping projects earn credits for energy efficiency and materials reuse.
Design Trends and Creative Expression
Patterned Play
Contemporary façades often embrace parametric design, using perforated metal panel arrays to convey cultural narratives or environmental data. In Miami, motifs inspired by ocean waves, mangrove roots, or Art Deco heritage add local resonance.
Color and Finish
Anodized, powder-coated, or fluoropolymer finishes grant bold hues that endure sun exposure. Neutral metallic tones or vibrant accent colors can transform a building’s identity.
Depth and Shadow
By offsetting panels or angling louvers, designers amplify shadow play throughout the day. This shifting geometry enlivens plain façades and responds to Miami’s changing light.
Integrated Lighting
LED backlighting behind perforated metal panels or tucked beneath louver edges introduces nighttime drama. Programmable lighting systems enable dynamic color shifts for events or wayfinding.
The Installation Journey
Bringing a façade vision to life involves several critical stages:
- Concept and Design
Collaborate with architects, engineers, and fabricators to finalize panel layouts and louver placement. Digital mock-ups and model studies validate aesthetics and performance. - Mock-up and Testing
Fabricate a representative façade section—complete with all intended finishes and mounting details—and subject it to wind, water, and structural testing in-house or via third-party labs. - Fabrication
Precision-cut panels and louvers are manufactured under controlled conditions. CNC punching or laser cutting ensures exact hole patterns, while roll-forming or extrusion produces consistent louver blades. - Site Preparation
Inspect substrate conditions, confirm anchor locations, and apply corrosion-resistant coatings to embedments. Coordinate with general contractors to sequence work and protect finished surfaces. - Installation
Using adjustable rails, standoffs, or concealed clips, installers mount panels and louvers according to engineered shop drawings. Site tolerances are fine-tuned to maintain uniform gap widths and alignment. - Quality Control
Post-installation inspections include thermal imaging to spot air leaks, water spray tests for infiltration checks, and torque audits on anchor fasteners. - Handover and Maintenance Plan
The installer provides as-built documentation, maintenance guidelines, and warranty information. Routine cleaning schedules and inspection protocols sustain long-term performance.
Cost Considerations
Budgeting for a high-performance façade requires balancing initial investment against lifecycle value:
- Material selection: Aluminum panels cost less upfront than specialty alloys, but long-term corrosion resistance and finish warranties may justify higher-quality metals.
- Pattern complexity: Intricate perforation layouts incur higher fabrication costs. Simple geometric repeats streamline production.
- Louver type: Fixed louvers are more economical than operable systems with actuators and controls.
- Installation logistics: High‑rise access, crane lifts, and site conditions can add to labor costs. Early coordination minimizes surprises.
A reputable installer will provide transparent pricing, value-engineering suggestions, and clear delineation of scope to avoid hidden fees.
Conclusion: Elevating Your Miami Project
Perforated metal panels and architectural louvers blend performance, durability, and design freedom—qualities that resonate deeply in Miami’s dynamic architectural landscape. When executed by an experienced, detail‑oriented façade installer, these systems deliver:
- Robust protection against sun, rain, and wind
- Enhanced occupant comfort through shading and ventilation
- Striking visual identity with custom patterns and finishes
- Sustainable solutions aligned with green building standards
For architects, developers, and building owners ready to transform their next Miami project, partnering with a skilled façade installer is the first step toward a visually compelling, high‑performance exterior. Carefully vet local expertise, demand rigorous testing and engineering support, and embrace the endless creative possibilities offered by perforated metal panels and architectural louvers. Your building’s next chapter begins at the intersection of art and engineering—choose wisely, and let your façade make a statement that stands the test of time.